For many companies, forklifts are indispensable. With the help of these machines for material handling, of various shapes and weights, the flow of palletized goods between different zones in the warehouse is streamlined.
Although the first forklift models based on the technology of goods lifts date back to the mid-19th century, the first models comparable to today’s only appeared at the end of World War I. In 1923, the first model of this type of device was made at Yale in the United States. It was powered by hydraulic energy and equipped with a cabin for the driver, forks, and a mast.
What criteria should be considered when choosing a forklift?
The choice of forklift depends on several criteria, each tailored to a specific warehouse or type of installation. Other factors to consider are the type of drive; internal combustion such as diesel, gasoline, or gas, or electric drive such as lead-acid or lithium batteries. This is a particularly important factor because it determines whether the forklift can be used indoors: electric forklifts are primarily used indoors to avoid exposing warehouse workers and goods to the gases released by forklifts running on diesel, gasoline, or gas.
When choosing a forklift, the layout of the warehouse must be taken into account, which refers to the arrangement of storage systems in the facility and the width of the aisles. Simply put, it is normal for an aisle to be between 3.20 and 3.50 meters wide when using a counterbalance forklift. The width of the aisle determines the choice of forklift model, depending on the type of mast: for example, a reach truck does not need to turn within the aisle because the board to which the forks are attached can rotate fully, allowing goods to be accessed from both sides of the aisle and also straight ahead.
The height of the forklift depends on the characteristics of the installed warehouse racking and the weight of the goods, as not all machines have the same lifting capacity. The manufacturer specifies the maximum weight for each forklift model that can be lifted.
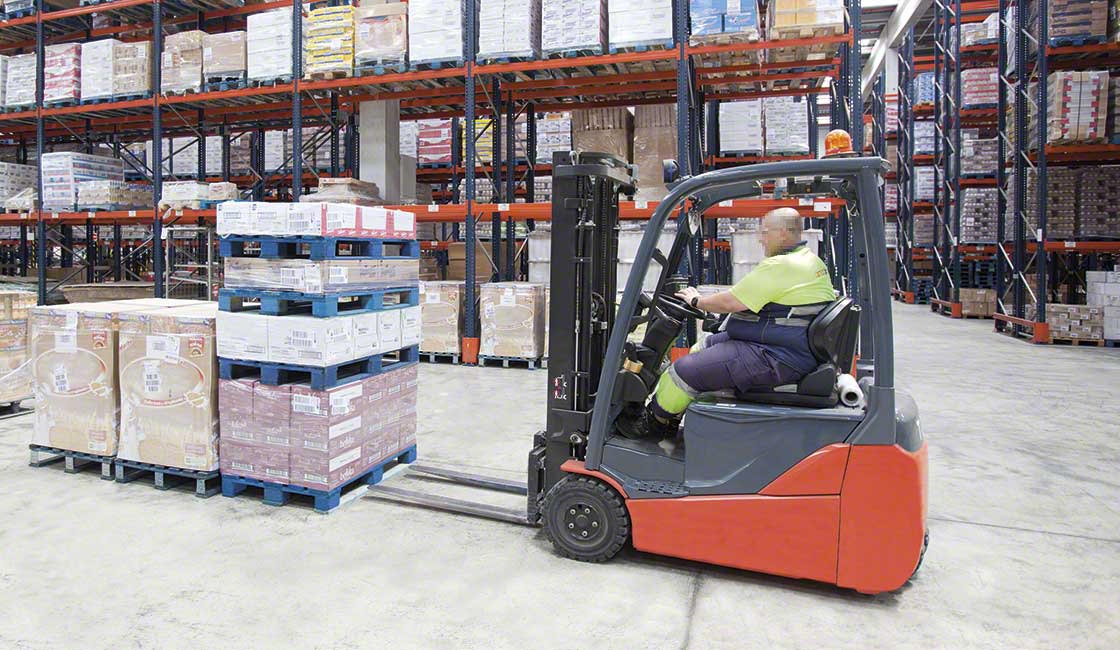
Forklifts by Warehouse Type
The type of forklift used in a warehouse depends, among other things, on the chosen storage systems, the layout of the aisles, and the load units that need to be handled. There are several types of forklifts to choose from, depending on the structure and functionalities, such as a reach truck, counterbalance forklift, or a tridirectional forklift. Below is an overview of the main forklift models, classified by warehouse type:
Counterbalance Forklifts for Traditional Warehouses
The counterbalance forklift is the most commonly used due to its great versatility. It can be used to load and unload trucks, move load units in or out of the racking systems, or improve internal material flows. While this forklift is used in all types of storage systems, it is most suitable for warehouses equipped with traditional pallet racking.
Reach Trucks in Warehouses with Highly Varied Goods
In warehouses where homogeneous goods are stored, drive-in racking for pallets is usually used, where forklifts drive into the racking themselves. Therefore, the use of reach trucks is often recommended, as the seating position improves the driver’s visibility when reversing.
Tridirectional Forklifts in Warehouses with Racking for Compact Storage of Diverse Goods
In facilities where a large variety of goods is processed and the available space is simultaneously optimized, such as in cold storage rooms, it is common to install movable racking systems that allow goods to be stored more compactly while keeping each pallet directly accessible.
Reach trucks are generally used in these types of warehouses, as they can operate in narrower aisles than counterbalance forklifts, typically between 2.70 and 2.90 meters wide, and can lift load units up to 10.5 meters high. In even narrower aisles, these machines can be replaced by bi- or tridirectional forklifts, which can operate in aisles ranging from 1.50 meters to 1.90 meters wide.
Side Loaders or Side Forklifts for Long Load Units
If the goods are long or large, such as pipes or profiles, side loaders or side forklifts are used, as the lifting system ensures stability, and they can move both forward and sideways without needing wide aisles. These forklifts are combined with cantilever racking, specifically designed for storing such load units as they have support arms.
Automated Guided Vehicles (AGVs) in Warehouses with Predefined Goods Flows
Warehouses with regular returning material flows, such as warehouses connected to a production center, can opt for automated guided, induction-guided, or laser-guided vehicles. This is the case in the warehouse of the pharmaceutical multinational Novartis in Stryków, Poland, which uses automated guided vehicles (AGVs) to move goods between the warehouse and the production center.
Automated Guided Vehicles (AGVs) are vehicles used in warehouses and factories, which automatically follow a predefined route. In logistics distribution centers that process a large number of orders, material flows can be automated by replacing induction or laser-guided vehicles with roller conveyors.
Order Picking Trucks in Warehouses for Order Picking and Consolidation
Manual pallet trucks and stackers are often used in warehouses for order picking, but they are not really considered forklifts. Order picking trucks, which are widely used in these environments, could also be placed in this category. There are several order picking trucks on the market that make it easier to pick orders from the first two or three levels of the racking. These machines can move only one pallet at a time but can be equipped with longer forks, up to 3.30 meters long, allowing several pallets to be moved at once. Or they can be equipped with an order picking truck.
Automation: Warehouses Without Forklifts?
The gradual replacement of forklifts by automated solutions has led many companies to consider automating processes, particularly repetitive tasks, to speed up the movement of goods. This is the conclusion of the latest research from the UK consultancy Brandessence Market Research, which points out that warehouse automation will grow by nearly 15% per year until 2027, exceeding 38 billion euros.
There are several solutions on the market that can automate the tasks of forklifts and improve the performance of logistics activities. For example, the loading and unloading of load units from racking systems can be automated by replacing tridirectional forklifts with automated tridirectional warehouse cranes. This solution speeds up material flows without requiring structural changes to the warehouse. This is the case at the automated logistics center of the pharmaceutical multinational Disalfarm in Rubí, Spain, which replaced its tridirectional forklifts with tridirectional warehouse cranes. Thanks to this change, the company now has continuous work cycles and has optimized available storage space.
Warehouses aiming for optimal efficiency and productivity can automate the material flows in part or throughout the entire warehouse, depending on the product type, the layout of the facility, or the logistical planning. Forklifts and manual storage systems can, for example, be replaced by warehouse cranes with one or two masts, which can operate in one or more aisles depending on the requirements of each warehouse. In automated facilities, roller conveyors are also installed between the different zones, speeding up the movement of goods.
In the automated high-rise warehouse of energy company CEPSA in San Roque, Spain, for example, locating and unloading load units from the racking is accelerated by seven double-deep warehouse cranes with two masts. Mecalux has also equipped the warehouse with a circuit of roller conveyors around the shipping area, which automatically move the goods to the loading docks.
A Forklift for Every Warehouse
Forklifts are essential for moving pallets from trucks to various zones of the warehouse. Which equipment is most suitable for your warehouse depends on several variables, such as the type of goods to be handled and the storage systems installed.
If you wish to improve the logistical performance of your warehouse and reduce the number of mistakes, feel free to contact us. One of our experts will advise you on the best solution for your company.