The order picking for e-commerce orders poses a logistical challenge for companies using online sales channels. Consumer trends such as omnichannel and the rise of q-commerce have prompted logistics managers to digitize processes to ensure optimal efficiency and productivity.
Due to ecommerce fulfillment, the complexity of logistics services has increased as there are various channels for interaction between the company and the customer, the so-called omnichannel. This consumer trend has also led to higher shipping costs, such as in the case of the last mile, and the additional costs for free returns. Ecommerce fulfillment requires perfect coordination between the sales department and the warehouse, ensuring that the catalog of different online sales points is synchronized with the physical stock. At this stage, any deviation can lead to stock shortages that may harm the company’s reputation.
What is e-commerce fulfillment?
E-commerce fulfillment is the logistics phase that encompasses all activities that take place in the warehouse from the moment an online order is placed until it is shipped. This phase includes processes such as inventory management, order picking, and packaging of products.
Order picking is the most costly activity in an e-commerce warehouse. The priority for this type of facility is speed, especially when it comes to shipping all orders as quickly as possible.
Inventory management is one of the most complex activities and is essential for ecommerce fulfillment. Just like pallets, warehouse bins have become a widely used load unit in recent years, particularly in e-commerce warehouses. As a result, companies have had to equip themselves with storage systems suitable for all load units. Add to this the increase in orders with multiple items, making order picking even more complex.
To ship so many different orders quickly, perfect organization of products and purchasing tasks is crucial. When the exact status of goods is known, they can be shipped on time, preventing delays and interruptions in order picking. It is also advisable to ensure efficient task distribution among warehouse workers so everyone can focus on processing as many orders as possible.
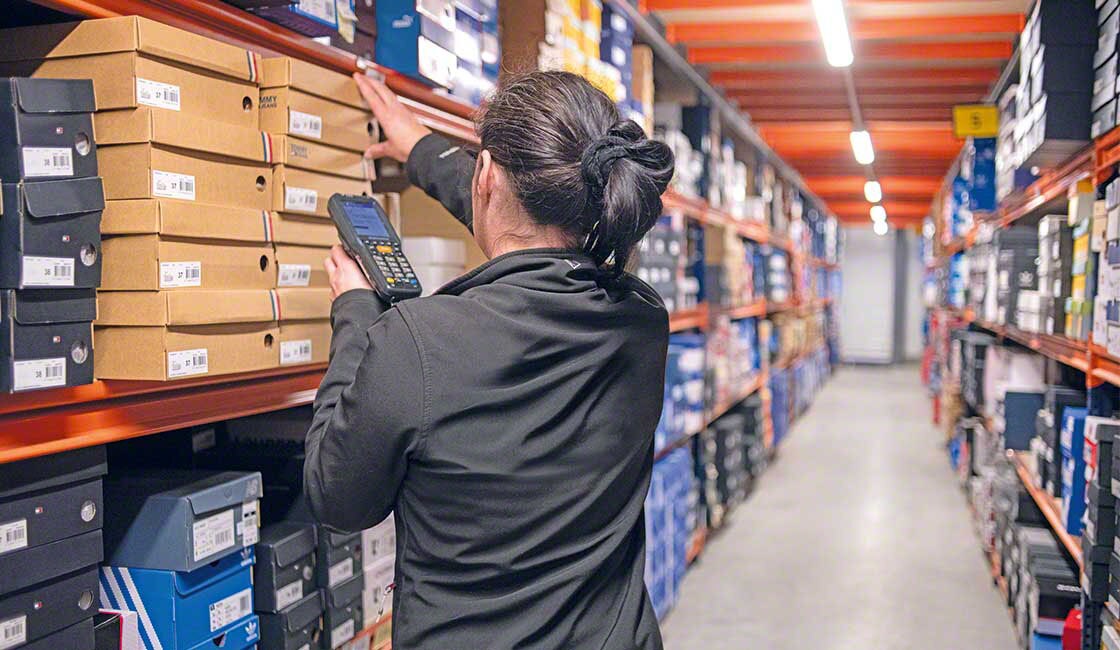
The Challenges of E-commerce Fulfillment
E-commerce has changed logistics centers, causing the layout of a warehouse tailored to online sales to generally differ from that of a traditional warehouse. The intrinsic characteristics of e-commerce logistics compel us to revisit the traditional warehouse to make it efficient for new activities. The main challenges of ecommerce fulfillment:
Shortening Lead Times
E-commerce forces companies to speed up warehouse processes to meet the standard 24-hour delivery deadline. Even when delivery times for some logistics services are shorter. Order picking is very dynamic, so the movements of warehouse workers need to be optimized for higher productivity. Warehouse Management Software plays a key role here, as it allows for a specific order picking strategy to be defined in advance based on the characteristics of the product and the warehouse. The WMS also assigns products to storage locations, based on rules and criteria established by the Logistics Manager.
Reducing Mistakes in Order Picking
For efficient e-commerce fulfillment, it is important to minimize mistakes as much as possible. Returns have indeed become a headache for companies doing business online. According to Deloitte, the number of returned orders has increased by 33% in the last ten years due to the rise of e-commerce. The consultancy predicted that e-commerce revenue would reach $573 billion in 2022, four times more than in 2008.
Warehouse Management Software (WMS) such as Easy WMS from Mecalux prevents 99% of mistakes associated with manual goods management. It directs operators during the order picking process and determines the most efficient strategy based on the warehouse layout and product characteristics.
Keeping and Synchronizing Stocks Up-to-Date
The development of sales channels and the variety of stored items increases the complexity of logistics activities like order picking. To ensure real-time inventory management, manual processes need to be replaced with Warehouse Management Software that can manage the entire facility’s activities.
Implementing WMS can be complemented with RFID readers or other tools for order picking, which prevent the loss of goods and increase the productivity of operators during order picking.
Preventing the Proliferation of SKUs
The specifics of e-commerce require logistical planning in which the turnover rate of items and their seasonality are analyzed. This limits the proliferation of SKUs, meaning the process of adding more Stock Keeping Units without prior demand studies, which complicates warehouse management and increases the likelihood of errors in order picking for e-commerce.
Optimizing Processes like Packaging and Kitting
In addition to complex tasks, warehouses focusing on online sales also need to adapt their packaging and shipping processes to the time of year. It is very common to personalize packages or labels for orders linked to specific dates such as Black Friday, Valentine's Day, or Cyber Monday. In e-commerce warehouses, this trend has been fully implemented, with specific areas reserved for personalizing products or orders based on customer preferences.
Efficiently Managing the “Last Mile”
Additionally, there are costs for the “last mile”. This logistical phase requires perfect organization to avoid extra costs that could jeopardize a company’s competitiveness. To achieve this, it is necessary to have the right tools that streamline communication between the warehouse and the various carriers. This is the goal of the advanced Multi Carrier Shipping Software module of Easy WMS, which fully manages the shipping process of goods.
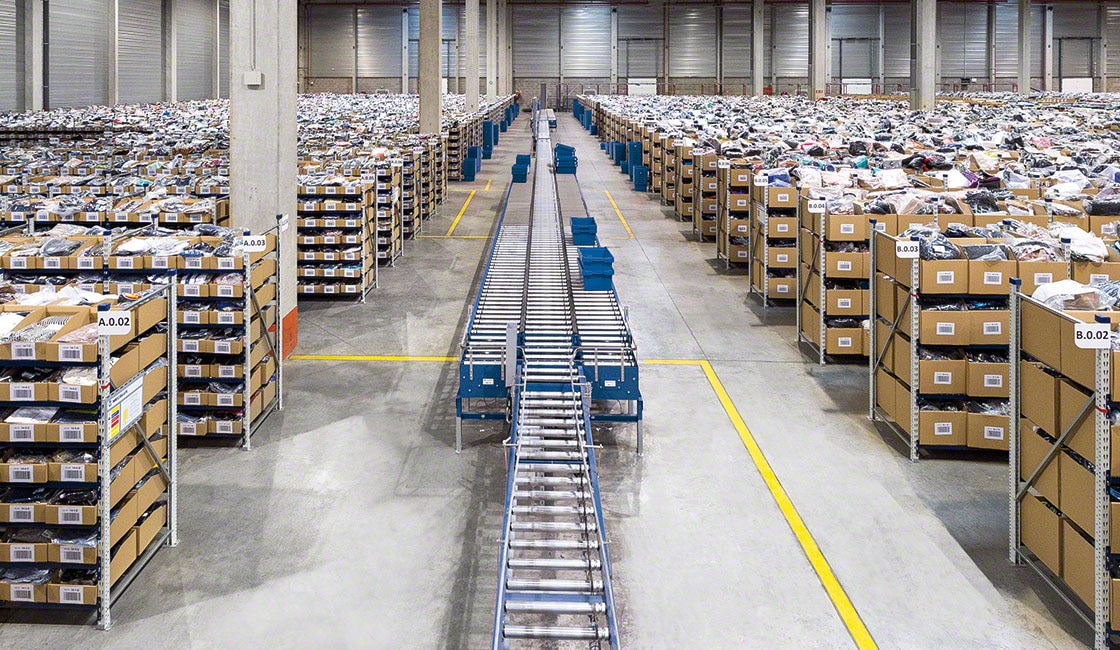
Storage Solutions for E-commerce Fulfillment
To optimize e-commerce fulfillment performance, businesses must make better use of the resources they have. How? By focusing on logistical strategies, ranging from opening new structures for order picking and shipping such as micro-fulfillment centers or dark stores, to implementing picking strategies like batch picking or pick to box, aiming to reduce costs and optimize operator movements.
There are several storage solutions available to optimize ecommerce fulfillment. Below are the main ones:
Manual Storage Solutions
Companies choose solutions suitable for the load units most commonly used in e-commerce, such as warehouse bins or trays. This is the case with French e-commerce store Deguisetoi.fr, which chose roller racking for boxes from Mecalux to accelerate order picking and improve the use of available storage space by 30%. Warehouses focused on online sales also use solutions such as industrial mezzanine floors, which increase the floor area and therefore storage capacity.
Conveyor Systems for Warehouse Bins
Another commonly used solution is replacing manual material handling equipment with conveyor systems for boxes to accelerate the goods flow in the warehouse. This guarantees a continuous supply of stock to the order picking zone. The online store Espace des Marques equipped its warehouse in France with a conveyor system for boxes installed by Mecalux, which, according to Vincent Beaufreton, Development Manager, “connects the different levels of the installation and speeds up the movement of goods.”
Order Picking Tools
Order picking can also be optimized with tools such as pick-to-light or voice picking. These increase productivity and reduce the error margin in order picking. Aghasa Turis, an e-commerce distributor of hardware, has installed pick-to-light and put-to-light systems in its warehouse in Spain to simplify and stimulate the work of warehouse staff. “Thanks to the pick-to-light and put-to-light systems, we have been able to increase the speed of order picking by 15%,” says Darío Alonso, CEO of the company.
Specialized Software
Digitizing logistical processes prevents mistakes associated with manual warehouse management. Mecalux's Easy WMS includes many advanced features suitable for e-commerce. For example, the Marketplace and E-commerce Platform Integration module synchronizes the company’s online catalog with the physical stock, preventing errors. WMS for e-commerce is a specific module that adapts warehouse activities to e-commerce. Using Supply Chain Analytics, the logistics manager can monitor various logistics KPIs and evaluate the warehouse's actual performance. The e-commerce company Global Freaks, specializing in figurines, has chosen the Marketplace and E-commerce Platform Integration, WMS for e-commerce, and Multi Carrier Shipping Software modules from Easy WMS to meet its growth projections. As a result, the company’s capacity to process orders has tripled.
Automated Order Picking
Order picking can be automated by equipping the e-commerce warehouse with robots such as the Miniload that can speed up the loading and unloading of goods. This system can be complemented with conveyor systems for boxes to improve the flow of goods to the picking stations. The tool manufacturer SAM Outillage has equipped its logistics distribution center in France with an automatic small goods warehouse. Thanks to automation, operational performance has improved, and productivity has increased by 25%. Candice Aubert, Logistics Manager, explains: “For the renovation of our distribution center, operators had to walk 10 to 12 km per day in the warehouse to find the items they needed. With the automatic small goods warehouse, the goods are automatically brought to the picking stations.”
E-commerce Fulfillment Requires Good Performance
Webshops must adapt their logistics to current consumer trends in the market as well as to the specific characteristics and standards of e-commerce. The key to staying competitive in the online sales sector is equipping the warehouse with both conventional and automatic storage systems so that orders can be processed more efficiently and, in particular, the number of order picking errors can be reduced.
By using Warehouse Management Software such as Easy WMS, 99% of mistakes made during manual order picking can be avoided, which is a significant advantage.
Would you like to fully benefit from the advantages of e-commerce and improve the performance of your warehouse? Don't hesitate to contact us; one of our experts will be happy to help you find the best solution for your business.