In this article, we present some examples of automated systems at companies that have installed Mecalux automated solutions to optimize the performance of their logistics operations.
Automated warehouses allow for the management, optimization, and acceleration of processes. More and more companies are choosing logistics automation, and according to a study by Global Industry Analysts, Inc., the market is expected to grow at a compound annual growth rate (CAGR) of 10.4% between 2020 and 2027.
The main driver for companies to robotize their warehouses lies in the many benefits it offers: high productivity thanks to a continuous flow of goods 24 hours a day, 7 days a week, lower maintenance costs due to less use of handling equipment, and continuous inventory management thanks to Warehouse Management Software (WMS).
Let’s take a look at the tasks that can be automated using Mecalux solutions:
Incoming and Outgoing Goods
Receiving goods and dispatching orders are two basic activities of a warehouse. In these areas, the daily goods flow is highest. On the one hand, goods receiving is the starting point for the flow of goods into the warehouse. On the other hand, shipping ensures the distribution of the required products.
These activities can be accelerated with automated truck loading and unloading systems, a solution that allows goods to be received and shipped quickly and safely through the warehouse.
The Spanish food company Grupo Siro has installed automated systems for handling incoming and outgoing products in its warehouse. In this case, it involves a large amount of heavy load units that often need to be loaded and unloaded.
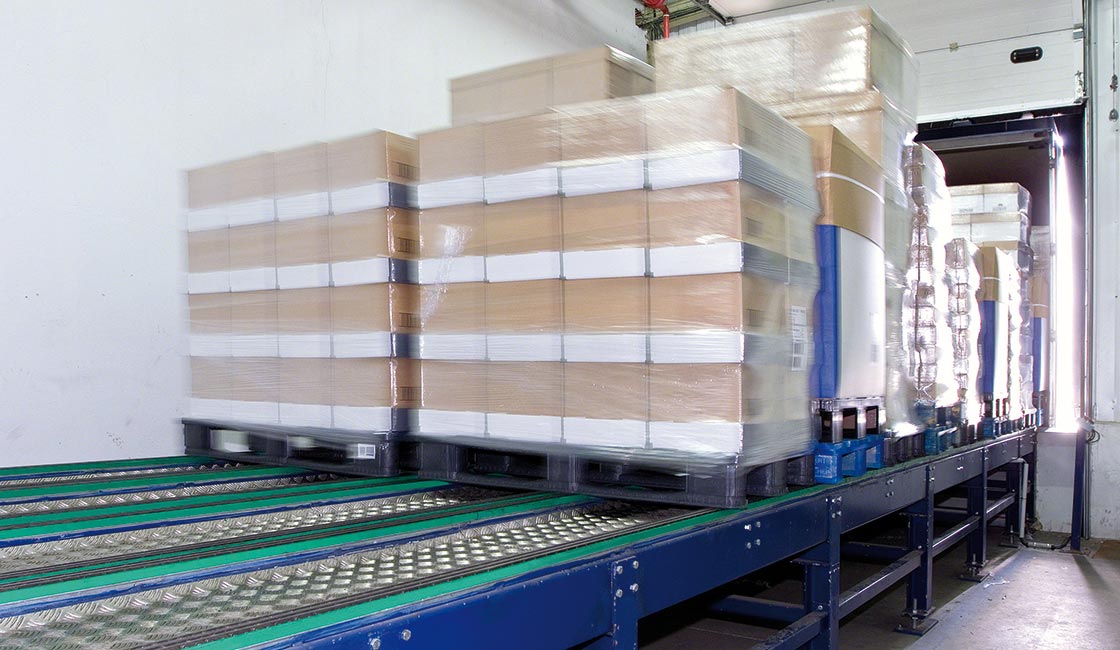
Goods Flows
For warehouse employees, moving load units is a very time-consuming activity. Roller conveyors are the most effective solution to facilitate the movement of products as they are versatile and allow for a large number of circuits, from a simple route of a few meters to more complex structures that connect different zones, floors, or buildings.
The distributor of nuts and other dried fruits, Tadım, for example, has a warehouse with automated systems in Turkey, where production lines are connected through a conveyor system. "We increased the number of daily deliveries by 73%," says Kemal Güler, Logistics Manager. The company receives an average of 1,000 pallets per day. The conveyors ensure a continuous flow of goods, minimizing the use of handling equipment and reducing the risk of accidents.
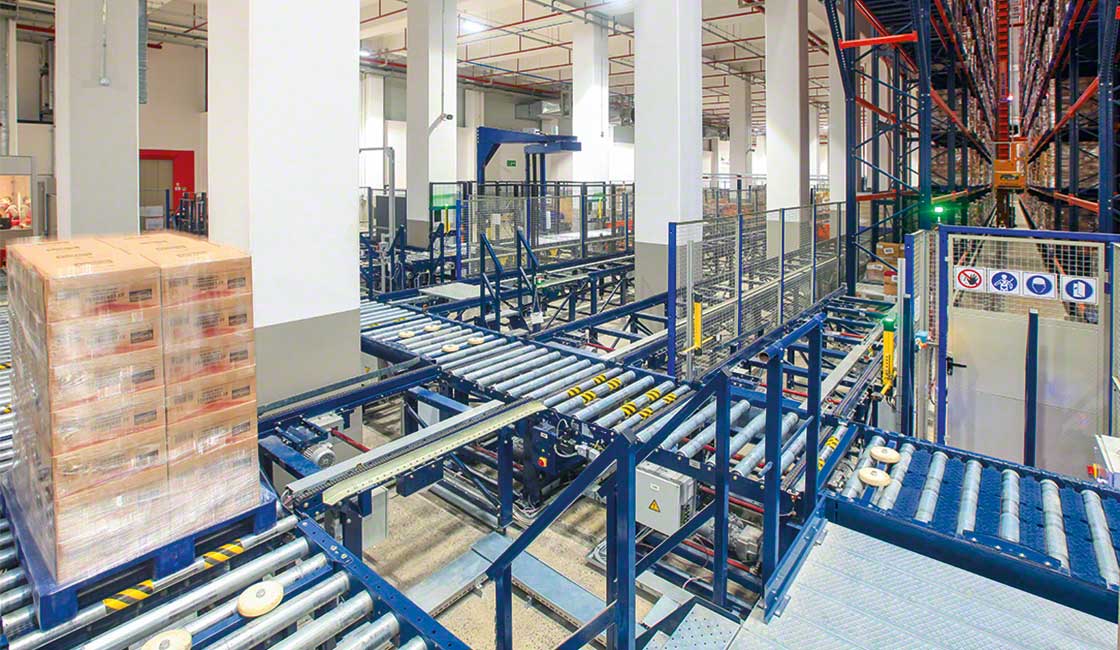
Another transport system used to connect different zones of the warehouse is the electric monorail systems (EMS). These are automatic trolleys or product carriers powered by an electric motor, moving along rails mounted either on the ceiling or the floor. The Polish juice manufacturer Sokpol benefits from this solution: two warehouses are connected to the factory via a fully electric monorail system from Mecalux.
Companies also use Automated Guided Vehicles (AGVs) or Autonomous Mobile Robots (AMRs) to connect different zones. The French paper manufacturer Clairefontaine uses several AGVs designed by Mecalux for internal transport in its warehouse. The company uses them to move goods from the production center to the warehouse or from storage locations to the shipping area.
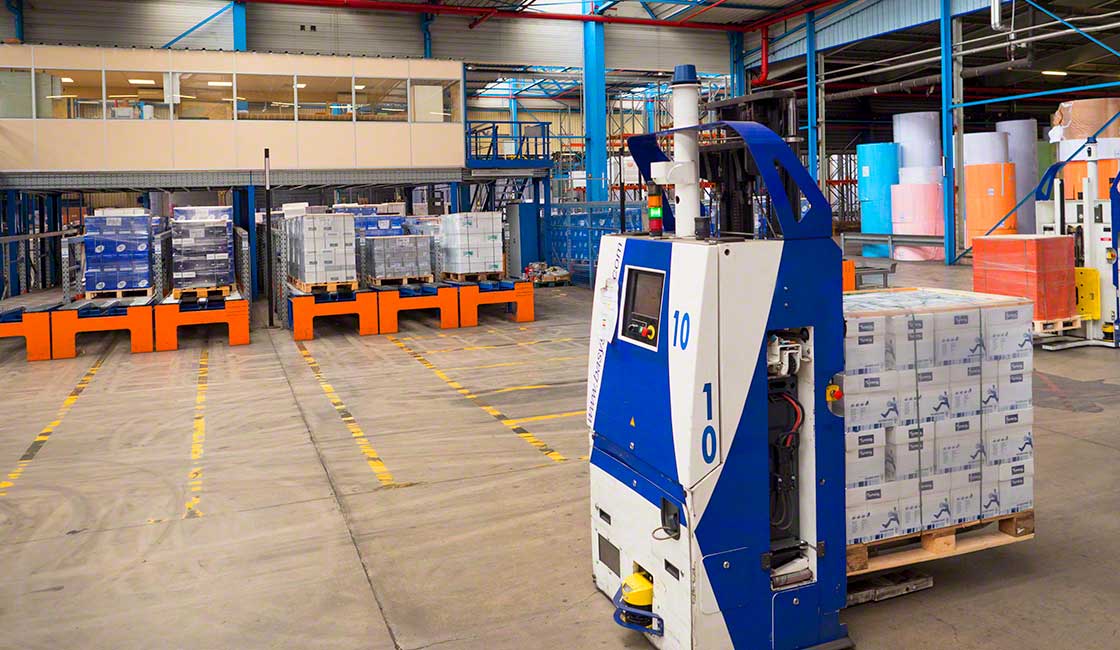
Goods Storage
The most representative examples of automated systems are those designed to automate storage itself, meaning the placement of load units at the assigned storage location.
Within this category, warehouse cranes stand out from other automated systems. This is a robot that moves through the aisles and independently loads and unloads pallets. In France, Schaal Chocolatier, a leading producer of high-quality chocolate, has an automated pallet warehouse designed by Mecalux. It is used to store products before they are distributed. The company decided to automate its logistics "so that traditional forklifts with drivers are no longer necessary," explains Raphael Dorbeau, Methods Department Manager.
Companies with large volumes of incoming and outgoing goods may choose another widely used automated solution: the automatic Pallet Shuttle system. This system uses an automatic shuttle to move through storage channels to load and unload pallets. This shuttle is moved to the desired storage channels using warehouse cranes or a warehouse truck. La Piamontesa, an Argentine company specializing in meat products, has equipped its cold storage facility with this storage system. “We had limited space, so we wanted to optimize it to store more products. After evaluating various options, we chose an automated solution,” explains engineer Diego Ghersi, Engineering and Projects Manager at La Piamontesa.
In warehouses where small items are stored, there is the option to install a Miniload. This operates similarly to a warehouse crane: the Miniload moves through every aisle and loads and unloads items from the warehouse racks without warehouse staff intervention, ensuring fast and smooth goods management and order picking. The Spanish beef producer Elaborados Cárnicos Medina has robotized its storage area with an automatic Miniload from Mecalux. According to José López, Operations Director, “The automated system has become essential for the production process, we couldn't do without it.”
Order Picking
Order picking is one of the most demanding tasks. To do so, companies apply the "goods to man" principle, where warehouse staff are stationed at picking stations and goods are brought to them via automated systems such as stacker cranes or conveyors.
The tool manufacturer SAM Outillage has optimized order picking thanks to Mecalux’s automatic Miniload, which allowed for the implementation of the "goods to man" method. Candice Aubert, Logistics Manager, explains: “Previously, operators had to walk 10 to 12 km per day in the warehouse to find the items they needed. With the automatic Miniload, goods are automatically moved to the picking stations.”
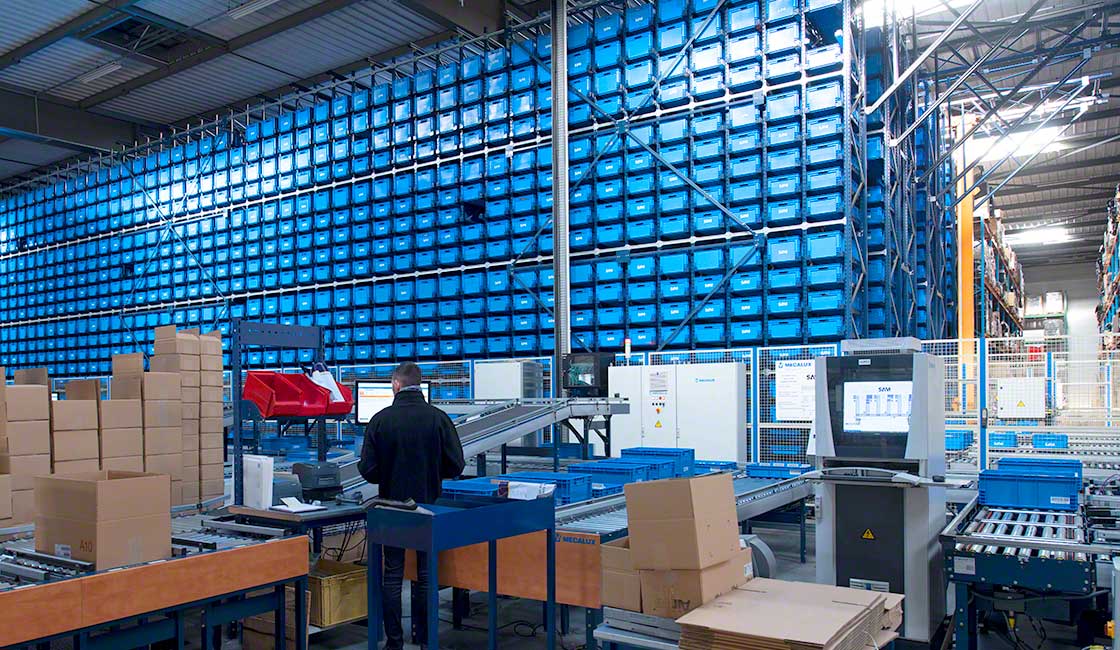
Warehouse Management
Good organization and warehouse management are essential to provide excellent service. With Warehouse Management Software, companies can manage products more logically and efficiently, leading to better performance.
Easy WMS has been implemented in more than 1,000 installations in 36 countries. The benefits of this program include inventory management, allowing for the status, location, and destination of goods to be tracked, and smooth product and information flows.
Maison François Cholat, a French company specializing in materials and tools for farmers, equipped its warehouse with Easy WMS to ensure complete traceability of its products. The sale and storage of phytosanitary products are two activities that are highly regulated in France and require full traceability since 2016. “We needed a WMS that could trace a product based on a specific item and capture important information about the products, such as production dates or batch numbers. This way, we can easily recall an item from the market if needed,” explains Morgane Cholat, Logistics Manager of the company.
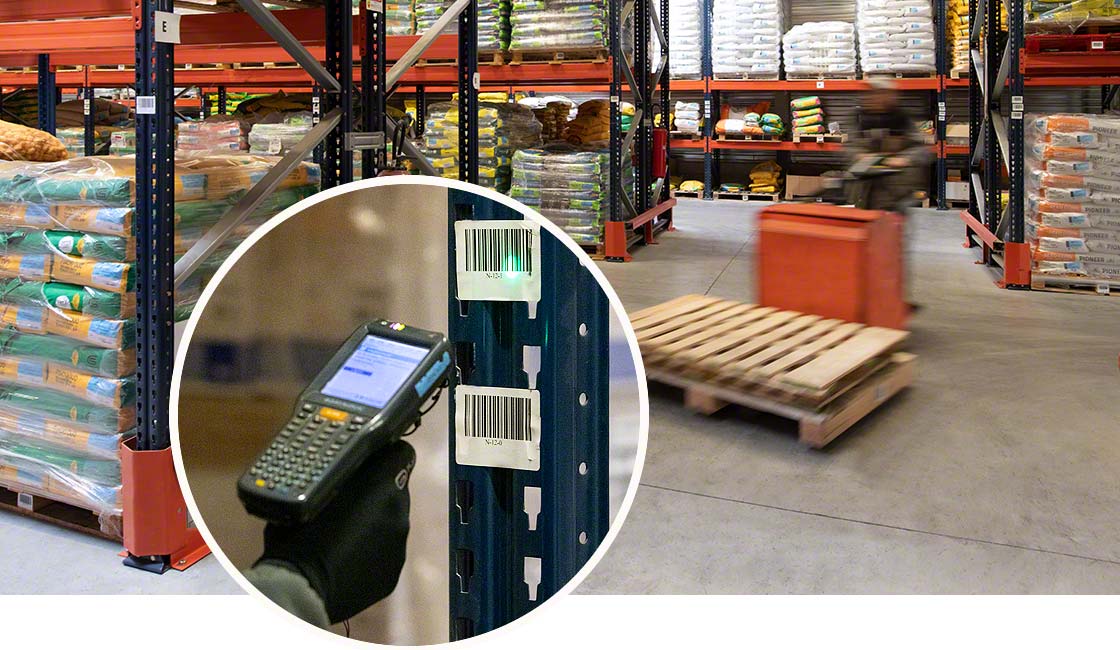
Automated Systems for Better Performance
Automated systems are solutions chosen by many companies to improve the performance of their operations. Warehouse cranes, conveyors, and Pallet Shuttle systems can be integrated into any warehouse to optimize goods flows.
Mecalux has automated operations for numerous warehouses. Are you also considering digitalizing and robotizing your logistics? Don’t hesitate to contact us for more information.